From gowning rooms to virtual twins, 바카라 배팅 법 and automation redefine quality control at Korea’s leading solid dosage facility
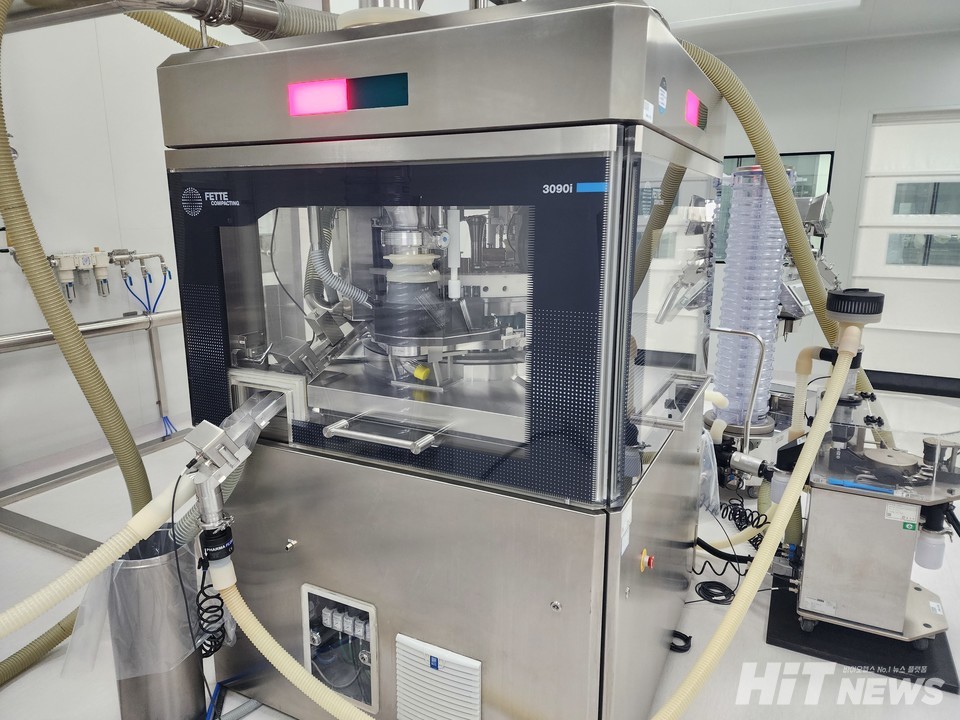
ChongKunDang’s Cheonan facility is redefining pharmaceutical manufacturing by integrating AI, big data, and automation into a unified digital platform. At the core of this transformation is the plant’s solid oral dosage line, where AI technology is actively used to enhance quality control.
To learn more about how 바카라 배팅 법 is applied and how accurate its quality predictions are, HitNews visited the site.
Upon arriving at the Cheonan plant at 2:00 PM on April 29, our team was greeted by a production staff member who promptly instructed, “Please remove all watches, earrings, and rings.” After removing accessories, we were given gowns and hairnets prepared according to our pre-registered clothing and shoe sizes.
Entering the production area wasn’t immediate. Several steps followed—including two full changes of clothing.
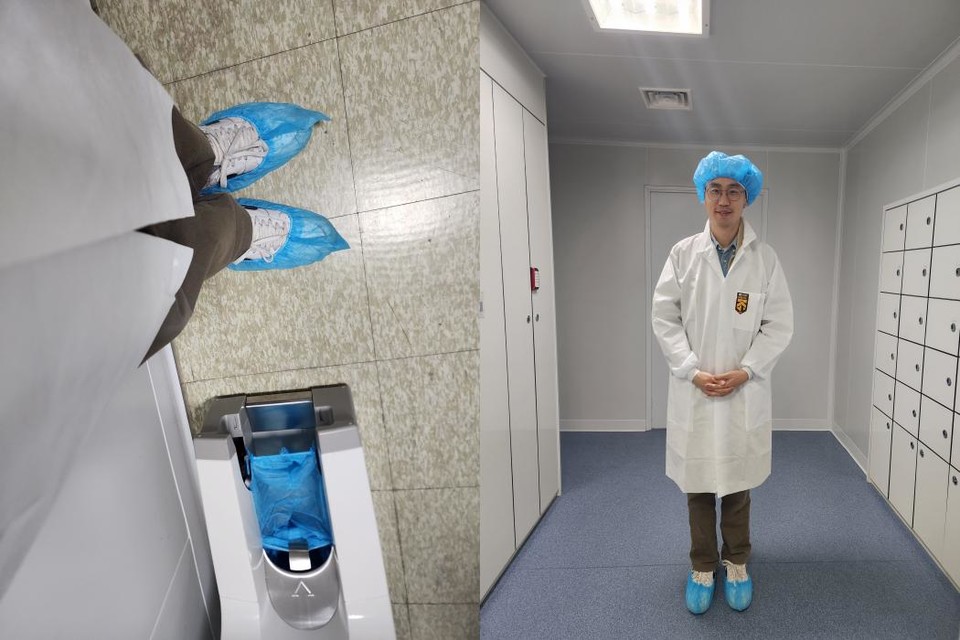
At the changing room, we first donned blue hairnets, white gowns, and face masks to prevent contamination. But before entering the clean zone, we had to change once more—this time into full-body disposable coveralls.
These high-necked, lint-free white suits, which had to be stepped into from the legs up, were cumbersome to wear. It was clear the daily effort required of ChongKunDang’s employees deserved acknowledgment.
As we passed through a hatch-like door that opened from the floor up, we stepped into the production area. A persistent white noise filled the air—so loud that nearby voices became difficult to hear.
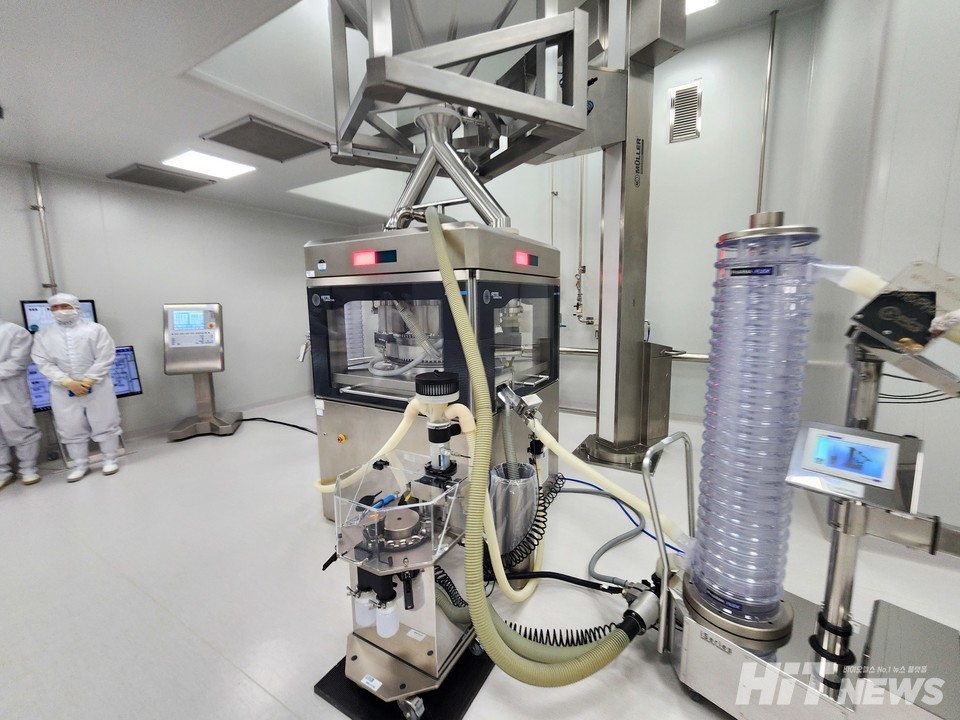
Signs marked every zone—gowning rooms, antechambers, and solvent storage. Through glass windows, we could see work proceeding steadily.
Inside the tablet compression room stood a towering machine nearly two meters high, wrapped in thick coils of cable. A transparent cylinder stood beside it.
“After raw materials are granulated into uniform particles, they are compressed here into tablets,” a plant representative explained. “Powder is fed between upper and lower punches, forming one tablet per half-rotation.”
He continued, “A vibrating step removes residual powder post-compression, followed by metal detection. Passed tablets are stored in drums. Some go to coating, while uncoated ones are sent to the warehouse.”
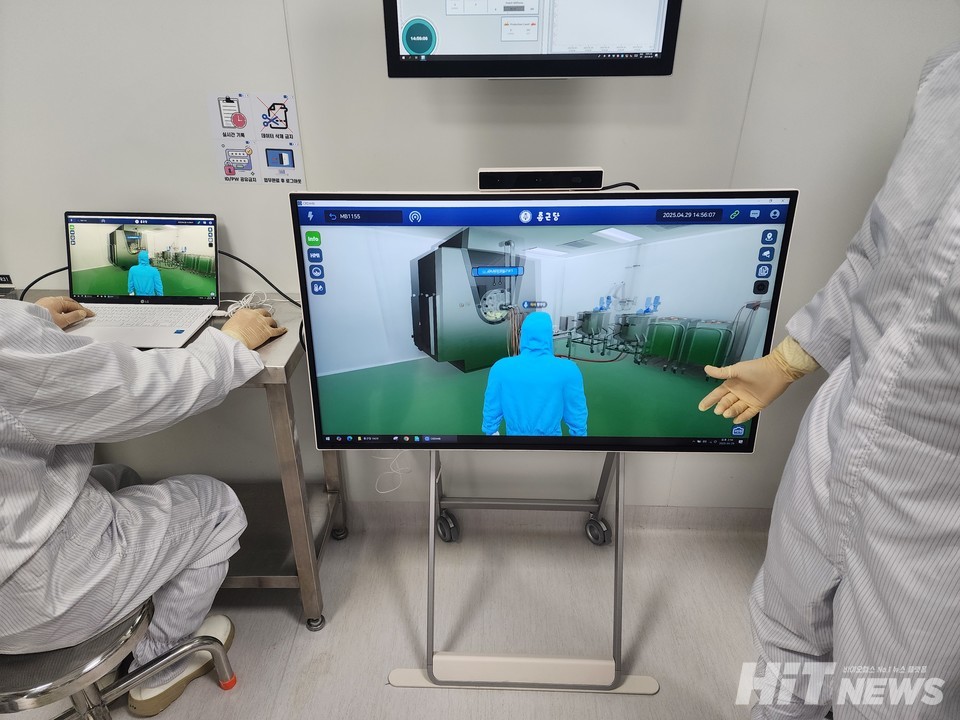
On nearby monitors, a virtual rendering of the plant came into view—complete with a moving avatar traversing rooms on the second floor. The scene was part of a digital twin system powered by AI.
“This metaverse platform lets us monitor real-time production data,” a ChongKunDang staff member explained. “Environmental data from the compression room is fed into the AI system, which also collects compression force, speed, and other quality metrics directly from equipment.”
Clicking the AI button opened a window titled “AI Quality Prediction Results,” displaying parameters for Lipilou 10mg—including predicted defect rates, mass variation, content uniformity, and dissolution metrics, all benchmarked against acceptable ranges.
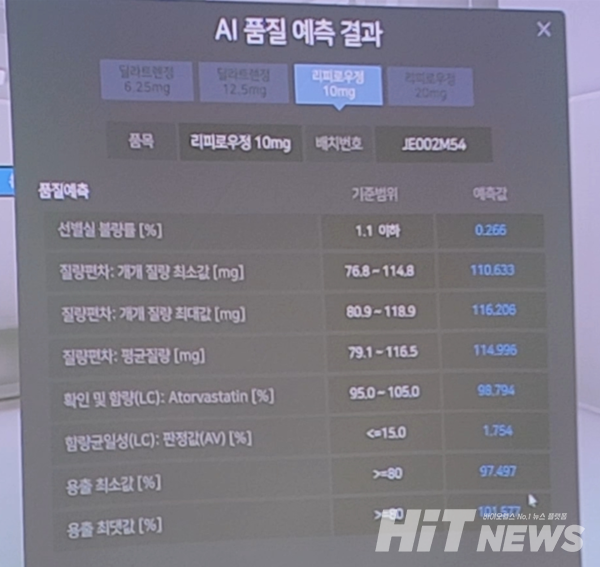
Hyunwon Byun, Head of Production at ChongKunDang, explained, “This system allows us to predict product quality during compression—without relying on physical testing.”
He added, “Conventional QC requires sampling and lab analysis. But once the AI model is trained, we can forecast quality in real time. The results have been more accurate than we anticipated.”
The system can even reverse-engineer process settings based on target defect rates. “Say we input a defect rate of 0.01%. The AI suggests optimal press settings to meet that goal,” said Byun.
“By defining QTTPs—Quality Target Product Profiles—we can simulate and optimize production parameters during product development. This greatly streamlines quality assurance.”
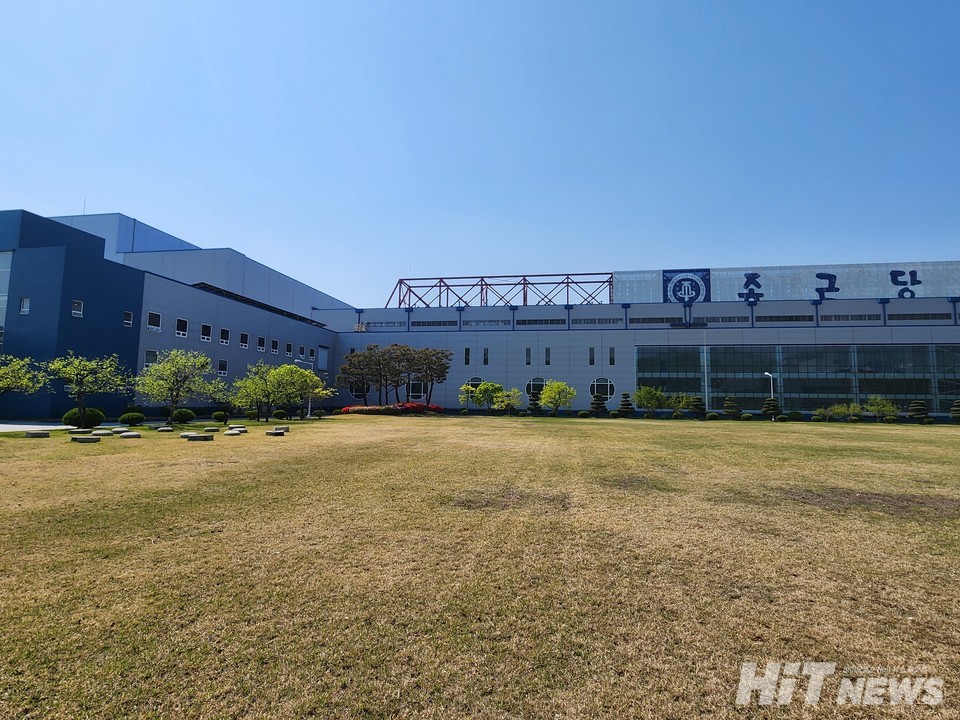
Spanning over 570,000 square feet, the Cheonan plant has long led Korea’s pharmaceutical manufacturing. Since its founding, it has used a Point of Production (POP) system to digitally manage operations across the entire manufacturing chain—from raw material intake to final product shipment.
All logistics, including movement of semi-finished and finished goods, are automated using unmanned guided vehicles (LGVs) connected to a central warehouse system. In 2013, cephalosporin and penicillin lines were separated to meet cGMP standards, and a dedicated biopharmaceutical line was added.
Today, AI is embedded across the facility—often invisibly. ChongKunDang executives are already exploring ways to integrate AI into GMP systems and proactively anticipate regulatory developments.
Their long-standing commitment to technological innovation is clearly alive and well.